L’ottimizzazione del ciclo di produzione nell’azienda Elettronica
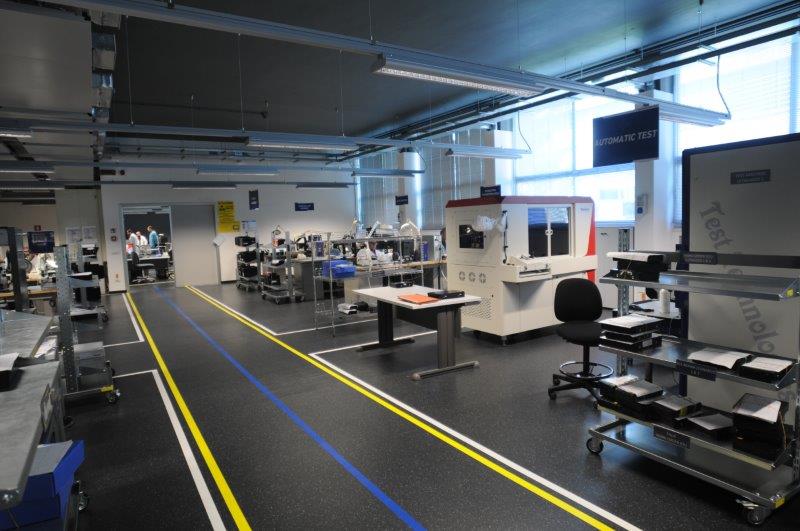
di Ermanno Petricca*
Elettronica è una azienda che opera nel settore della Difesa Elettronica e che ha come unica missione offrire soluzioni innovative che garantiscano la sicurezza delle persone, dei beni e delle informazioni negli scenari operativi più complessi.
La Società svolge attività di ricerca, studio, progettazione, sviluppo, realizzazione e vendita, sia in Italia che all’estero, di componenti e di sistemi integrati e relativi software, che siano idonei a rilevare, elaborare, generare e emettere segnali elettromagnetici incluso l’infrarosso, acustici o di altra natura, per la difesa di piattaforme di terra, navali e aerospaziali.
E’ un’azienda nata più di 60 anni fa, precisamente nel 1951.
Ci sono tanti modi per leggere la storia di un’azienda che ha saputo essere così longeva (sta vivendo la ‘terza’ generazione, in un periodo in cui l’età media delle aziende italiane non supera la prima): uno di questi è osservare lo sviluppo della Società attraverso l’evoluzione del suo ciclo produttivo.
Senza andare troppo indietro nel tempo, nei primi anni Novanta il modello produttivo perseguito da Elettronica era orientato a fare tutto in casa, dalle viti e rondelle fino alle casse per gli imballaggi delle spedizioni e, di conseguenza, la Società aveva al suo interno tutte le facilities necessarie, come l’officina meccanica, i laboratori tecnologici e persino una falegnameria.
Tale modello è stato progressivamente abbandonato con una decisa accelerazione soprattutto negli ultimi anni. Il risultato complessivo, apprezzabile nei numeri (i volumi di produzione infatti sono triplicati in un perimetro di risorse necessario ridotto del 25%), è maturato grazie ad un forte cambiamento dei processi, degli ambienti, della struttura gestionale e delle modalità di lavoro.
Di seguito una sintesi dei principali elementi distintivi della “trasformazione”.
Le tecnologie produttive core
Il modello produttivo al quale si è arrivati prevede la presenza in Elettronica di tre tecnologie: Microelettronica, Videodigitale, Unità e Sistemi.
Le prime due sono le tecnologie di base dei sistemi della Società e trattandosi di elementi core dello sviluppo, si è seguito il criterio del “si fa dove si pensa”. Ciò chiaramente non esclude la possibilità di rivolgersi all’esterno, ma la presenza dei laboratori di produzione garantisce il mantenimento ed il rafforzamento della competenza.
La terza tecnologia, che prevede la realizzazione del prodotto finale destinato al Cliente e tutte le facilities necessarie per i test, le qualifiche, le validazioni, è e resterà una tecnologia interna, per la diretta vicinanza con il Cliente.
La relazione tra Manufacturing e Engineering
La caratteristica del mercato in cui Elettronica compete richiede lo sviluppo continuo di nuovi prodotti che transiteranno nelle linee produttive, interne o esterne.
La relazione tra Manufacturing e Engineering è la chiave vincente per fornire prodotti competitivi in termini di costi – prestazioni. Momenti di confronto e condivisione strutturati tra le Funzioni, volti a verificare l’applicazione delle regole di montaggio e collaudo (i.e. design rules), la scelta dei componenti mediante una preferred part list, l’aggiornamento delle schede di producibilità consentono di perseguire l’obiettivo didesign for manufacturing, perchè la prima ottimizzazione di un ciclo produttivo nasce proprio da lì!
Gli Ambienti di lavoro
A partire dal 2012 si è lanciato un importante investimento per integrare in un’unica area i diversi laboratori, dando vita ad un unico ambiente di Produzione guidato dai principi di lean manufacturing, per avere lo stesso standard e la stessa metodologia pur nella molteplicità delle competenze; un ambiente paperless, dove tutte le informazioni necessarie per l’esecuzione sono disponibili in digitale, spingendo fin dove possibile sull’automazione dei processi.
I benefici ottenuti (riduzione del 50% del lead time e del 30% del waste) oggi ripagano ampiamente l’investimento fatto.
La Gestione operativa
In un contesto estremamente dinamico, le linee di produzione prevedono prodotti consolidati e prodotti di piccole serie o prototipi, in funzione del portafoglio ordini della Società. In particolare, oggi stiamo transitando da una predominanza di prodotti consolidati ad una prevalenza di nuovi prodotti. Per citare qualche numero, nell’anno in corso stiamo gestendo circa diecimila codici diversi, tra semilavorati e componenti. Cambiare scenario senza soluzione di continuità è possibile se si agisce in anticipo sulla flessibilità operativa, trasformando una linea di prodotto in una cella di processo o viceversa; sulla formazione per distribuire il know how; sulla organizzazione, introducendo nel reparto produttivo risorse di pianificazione e di ingegneria di produzione che vivono e condividono il ritmo quotidiano delle attività.
In questo contesto più che la massimizzazione dell’utilizzo degli equipments si ricerca la massimizzazione dell’on time delivery, il key perfomance indicator che più di ogni altro evidenzia il time to market, e la minimizzazione degli aspetti di poor quality, elementi determinanti di questo business, insieme ad una riduzione (condizione vera in qualsiasi contesto) dei costi ricorrenti.
La Supply Chain
Un elemento importante, nel momento in cui si è stabilito il dimensionamento interno ottimale, è stato la definizione della supply chain nella gestione del built to print. Dopo una fase transitoria, la scelta è caduta su un ristretto numero di fornitori, agili, capaci di rispondere prontamente alle nostre richieste, di recepire le nostre indicazioni arricchendo al contempo il loro know how e di essere propositivi nel segnalare proposte di miglioramento vantaggiose per entrambi. In sostanza, più partner che fornitori!
Le Risorse Umane
Last but not least, le Risorse Umane. Quando si affronta questo tema, il rischio è di cadere nel retorico o nel déjà vu, ma lo corriamo volentieri perché in Elettronica siamo fermamente convinti che non può esserci nessuna trasformazione positiva senza il pieno coinvolgimento di tutto il personale, a tutti i livelli. Questo il motivo per cui, a fianco delle tante iniziative fin qui illustrate, abbiamo un’attenzione costante all’engagement delle nostre persone e al benessere sul luogo di lavoro.
A questo punto è naturale porsi la domanda: i prossimi anni come saranno? Quali opportunità potranno essere colte nell’epoca della Industry 4.0?
Certamente non vogliamo aspettare alla finestra. Alcune iniziative sono già in corso, altre sono in fase di avvio, su temi come l’additive manufacturing, la realtà aumentata nei montaggi complessi, la digitalizzazione dei controlli visivi, la creazione di modelli predittivi per l’eliminazione del waste piuttosto che la rilevazione dei bottlenecks in scenari complessi e altro ancora.
Come immaginare allora il futuro della produzione? Arriverà forse un giorno in cui l’Azienda riceve un ordine dal cliente, lo traduce simultaneamente in un manufacturing data package e lo consegna ai laboratori che, attraverso macchine 3d, lo realizzano nell’arco di un solo giorno?
Se è così, è certo che in quel giorno sarà ancora più impressionante di oggi pensare che un tempo, nemmeno troppo lontano, eravamo tutti impegnati a realizzare viti, rondelle e casse di imballaggio.
*Ermanno Petricca è il Direttore di manufacturing & Industrial Processes

RedazioneVedi tutti gli articoli
La redazione di Analisi Difesa cura la selezione di notizie provenienti da agenzie, media e uffici stampa.